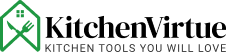
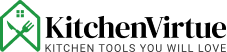
Canadian Owned · Canadian Pricing · Free Shipping over $95 · Price Guarantee · Worry-Free Returns · Gift Cards Available
Founded in 1887 and based in Effingham, Illinois, John Boos is one of the oldest manufacturers of premium quality foodservice equipment and butcher blocks in the country.
It was in his Effingham blacksmith shop that founder Conrad Boos developed what would become the original Boos Block. Having harvested sycamore from local wooded areas, Conrad then processed it in his sawmill and brought it to his blacksmith shop for finishing. That first block of sycamore slab placed on three legs would function as a block to absorb the shock of a smith’s hammer against the anvil. A local butcher, having seen and admired Conrad’s block, became intrigued and requested one for his meat market. Conrad’s son, John, would fulfill the request and, in turn, take the John Boos brand into the infancy of its more than 130-year reign of serving customers in the commercial market sector.
1887
Founder Conrad Boos harvested Sycamore from wooded areas around Effingham, IL, processed it at his sawmill, and then brought it to his blacksmith shop for finishing. The first innovation was a sycamore tree placed on three legs to absorb the shock of the blacksmith’s hammer against the anvil. When the local butcher saw and admired the innovation, he realized that he could use one in his meat market. Conrad’s son, John, adapted the idea and handcrafted himself his own butcher block.
1892
Boos family sells John Boos & Co. to a German immigrant named Adelbert Gravenhorst, an enterprising businessman who joined Conrad and John Boos to incorporate John Boos & Co. John F. Boos is elected the 1st President of the company. (Photo: Old pulley systems drive the machinery equipment.)
1895
John Boos & Co. location on Jefferson St. burned down and was rebuilt. Seven years later, John Boos & Co. expands and moves to a new location on South 1st St. in Effingham, IL.
1902
Adelbert Gravenhorst becomes President of John Boos & Co.
1929
John Boos & Co. successfully continues to grow its business despite the Great Depression Era. (Photo: Wood Plant Employees during the Great Depression Era.)
1941
John Boos & Co. expands product lines to include foodservice work tables and countertops as 80% of production is earmarked for WWII to equip military aid. (Photo: Hand Block Press)
1955
John Boos & Co. expands by adding a dry kiln, additional offices, and more manufacturing space. Shipping docks and warehousing is expanded and new products are created. (Photo: Mill Room)
1965
John Boos & Co. builds its first Stainless Steel Table. First ground combat action reported during the Vietnam War.
1970
John Boos & Co. reaches 100 employees. Customers continue to successfully grow in the foodservice industry as well as in the residential home market.
1980
John Boos & Co. metal plant burns down and is promptly rebuilt to meet the demands of stainless steel manufacturing.
1990
Stainless steel becomes popular in the kitchen with Boos Block Cucina Americana roll out consisting of integrated maple and stainless steel kitchen carts and worktables for the residential market
2000
Foodservice equipment successfully continues to expand into stadium kitchens. Metlife Stadium (New York Giants and Jets), Lucas Oil Stadium (Indianapolis Colts), University of Phoenix Stadium (Arizona Cardinals), Cowboys Stadium (Dallas Cowboys)
2012
John Boos & Co. celebrates serving their customers for 125 years and expands its markets for commercial and residential customers, and seizes new opportunities. Both wood and metal facilities reach milestones with production output. The company expanded with a move to a new corporate office of nearly 87,000 square feet combined with a new metal plant facility in Effingham, IL.
2014
After inhabiting the John Boos metal plant on S. Banker St. for three years, a new 42,000 square foot addition is added to the west side of the complex.
2015
The largest round butcher block in John Boos history is handcrafted. A massive, 84” diameter, 1,400 pound, solid black walnut butcher block, end grain construction, is handcrafted. The custom block is made in two pieces to fit through doorways.
2017
A new state-of-the-art John Boos wood plant is built on a 27-acre campus that includes John Boos’ stainless steel facility and the corporate headquarters. The wood plant features new, automated equipment, but the art of making Boos Block® cutting boards relies on the same proprietary process developed 130 years ago.
2018
The old wood plant, outlet store, corporate office and other John Boos buildings at the corner of S. Willow St. and E. Fayette are torn down after the new wood plant construction on S. Banker St. (Shown In Photo) The Factory Showroom & Outlet triples in size and a large sign marks the new location visible from Interstates 57/70 in 1703 Avenue of Mid-America, Effingham, IL. Showcased in the Factory Showroom is one of the original Boos butcher blocks that was crafted in the early 1900’s, and a history timeline shows information on the company’s beginnings from 1887 through to current day.
2019
New research out of the University of Illinois adds further credibility to the hygienic benefits of using Boos Block® cutting boards. The new study conducted by Mechanical Science and Engineering Professor Nenad Miljkovic and his research laboratory at the University of Illinois, found that the NSF listed Northern Hard Rock Maple cutting boards by John Boos & Co. kill bacteria. Data gathered by the team concluded that application of the NSF listed Boos Block Mystery Oil and Board Cream on the boards created an “antimicrobial, hydrophobic surface that decreased their surface bacteria to a ‘clean level’ in just three hours” without using recommended board cleaning procedures
2020
John Boos & Co. adapts and changes throughout 2020 as the shifts of the year present challenges during covid-19. A new emphasis is placed on cooking family meals at home. Boos Block cutting boards fill the demand for durable and sustainable hardwood prep surfaces. John Boos & Co. supplies stainless steel worktables to a temporary pop-up hospital and manufactures hygiene products such as mobile hand wash stations, hygiene stations, sanitizer stands, and worktables to assist in the demand of the pandemic
2023
A new Distribution Center in 2023 expanded the campus further, now spanning 32 acres with over 335,000 square feet. The company presently employs nearly 300 people and continues to hire on a regular basis to meet order demand.
No products were added to the Wishlist